Screwdrivers, the quiet champions of toolkits, wield versatility and functionality across diverse domains. From addressing simple household repairs to managing intricate industrial applications, these tools embody efficiency and precision. This exploration into the world of screwdrivers navigates their applications, significance, and their interplay with materials such as geotextile.
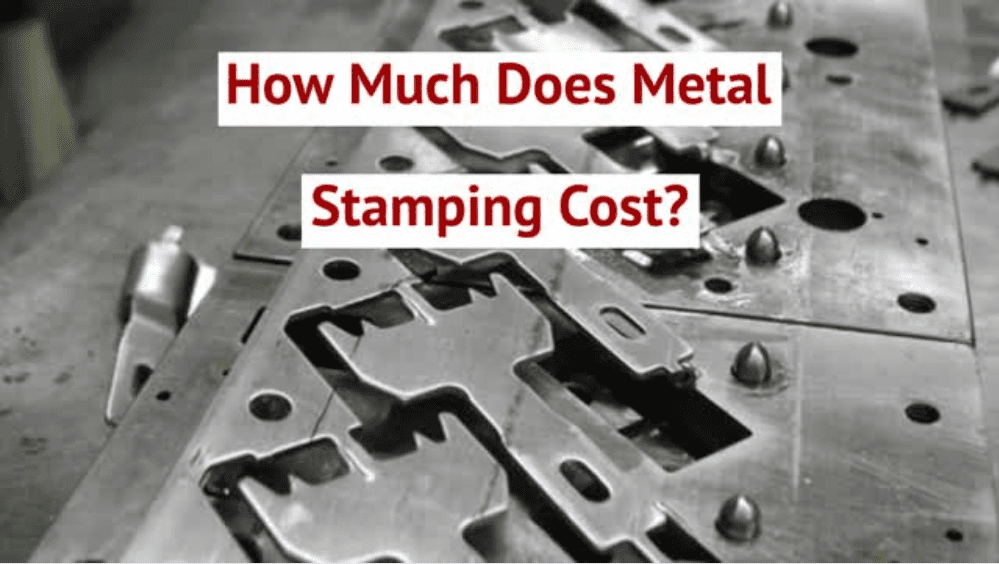
What are the different types of screwdrivers available in the market?
The market offers a myriad of screwdrivers tailored to specific tasks. Among the common types are flathead, Phillips, Torx, and Robertson screwdrivers. Each variation aligns with different screw head shapes, ensuring a secure fit and safeguarding against damage during tightening or loosening. Geotextile projects often demand specialized screwdrivers to firmly secure fixtures without compromising the fabric’s integrity.
How do screwdrivers contribute to various applications?
Screwdrivers wield substantial influence across industries. In construction, they assist in assembling structures, securing fixtures, and fastening materials like geotextile, crucial in erosion control and drainage systems. In the realm of electronics, precision screwdrivers delicately handle intricate components. Even in everyday life, they prove invaluable for furniture assembly, appliance repairs, and more.
What makes screwdrivers an essential part of any toolkit?
The adaptability and simplicity of screwdrivers render them indispensable. Lightweight, user-friendly, and versatile, they navigate various materials, including geotextile, showcasing extensive utility and cementing their status as a staple in both professional and DIY toolkits.
How can screwdrivers be optimized for better performance?
Selecting the appropriate screwdriver for the task is pivotal. Factors such as ergonomic handle design for comfort, magnetic tips for seamless screw handling, and durable materials contribute significantly. When handling geotextile tasks, opting for screwdrivers with corrosion-resistant coatings ensures longevity, particularly in outdoor environments.
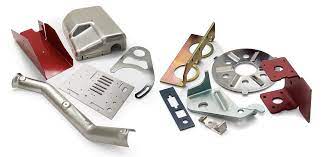
Applications and Relevance to Geotextile
Geotextiles, integral in civil engineering for soil stabilization, erosion control, and drainage systems, heavily rely on secure fastenings. Screwdrivers play a crucial role, in facilitating the precise installation of geotextile materials. Whether securing geotextile mats for slope stabilization or anchoring fabrics for drainage, the precision and reliability of screwdrivers ensure the effectiveness of these installations.
In summary, screwdrivers serve as indispensable tools across industries and daily tasks. Their compatibility with materials like geotextile underscores their versatility and significance in critical applications. Understanding their variations and optimizing their usage significantly enhances efficiency and precision, establishing them as cornerstones in any toolkit.
Next time you reach for a screwdriver, whether for a minor household fix or a complex geotextile installation, remember its impact transcends its size—it’s the key to unlocking precision and stability in myriad applications.